S.D.M Process
INTRODUCTION
This facility is to dry and minimize sludge generated from Water Treatment Plant or Waste Water Treatment Plant.
As treatment of sludge has been restricted and prohibited by global environment regulations, it is required to treat sludge effectively and environment-friendly.
However, it is difficult to enlarge existing technologies and facilities and they have many problems such as inefficient energy use, high processing cost.
Therefore, SAC has developed S.D.M Process and realized low processing cost and efficient energy use by compensating the existing problems.
We apply Moduler System which is possible to compose by units from small quantity to large-scale facility by adjusting the quantity of sludge produced from each site.
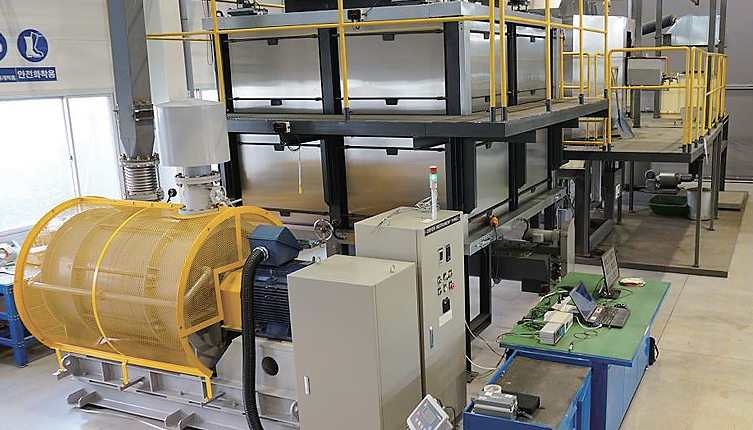
Drying Module Process
- Input Condition : Max. 80% of Moisture
Content - Output Condition : 3 - 10% of Moisture
Content
Features
- Continuous Type
- Full Automation by Industrial Computer
- Fit up Heat Exchanger
- Excellent Temperature Distribution
- Multi-Stage Blower
- Electric Heat or Fuel Burner Type
Advantages
- Excellent Energy Saving
(Reduction 35%) - Quality Improvement
Business
Water Slidge Drying Module Process
It engineers the whole process from minimizing sludge produced in water purification plant to reprocessing it into raw materials
(ceramics material, functional tiles, etc.).
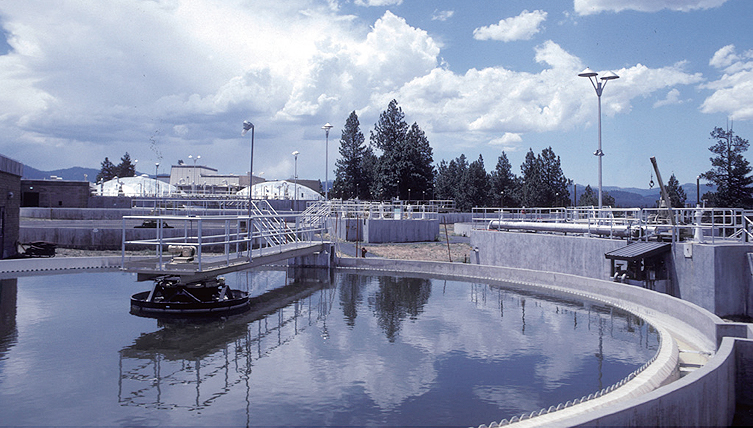
- Capacity 5ton/day - 100ton/day
- Input Condition : 75% of Moisture Content
- Output Condition : 3% - 30% of Moisture Content
- Process Temp : Dry Under 100℃, Retort 400℃ - 900℃
Sewage Sludge Drying Module Process
It engineers minimizing process of sludge produced in sewage treatment plant or in each business site.
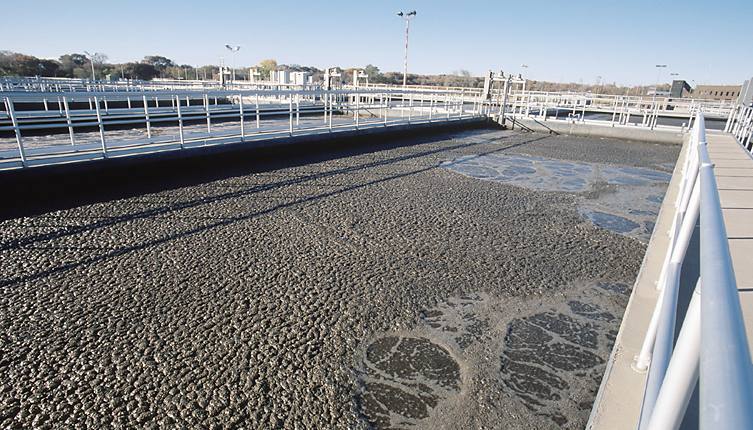
- Capacity : 5ton/day - 500ton/day (Depend on Process)
- Input Condition : 75% of Moisture Content
- Output Condition : Under 10% of Moisture Content
- Process Temp. : Dry Under 100℃, Kiln 300℃ - 400℃
Ore Drying Process
Submerged Arc Furnace (SAF) for ferro-alloy produces various kinds of ferro-alloy such as Fe-Mn, Fe-Ni, Si-Mn, Fe-Si and MG-Si melting raw materials down with electrical power.
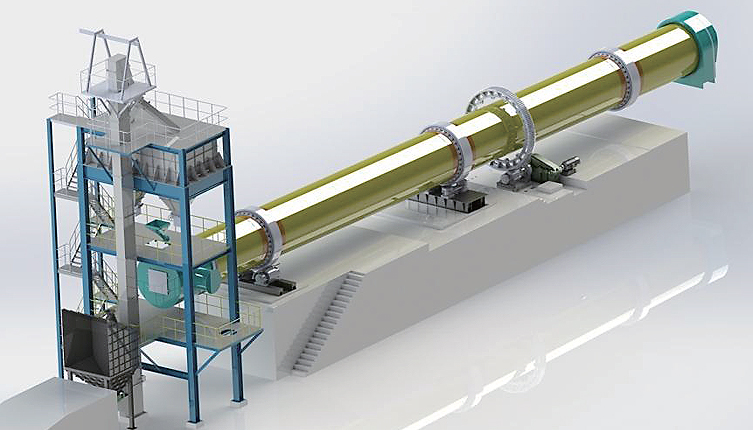
- Capacity 2,000 ton/day (Depend on Process)
- Input condition : 30% - 40% of Moisture Content
- Output Condition : Under 1% of Moisture Content
- Process Temp : Dry Under 100℃, Kiln 850℃ - 900℃